Enterprise Risk Management at Toyota
|
|
ICMR HOME | Case Studies Collection
Case Details:
Case Code : ERMT-006
Case Length : 15 Pages
Period : 2003
Pub Date : 2003
Teaching Note :Not Available Organization : Toyota
Industry : Auto and Ancillaries Countries : Global
To download Enterprise Risk Management at Toyota case study
(Case Code: ERMT-006) click on the button below, and select the case from the list of available cases:
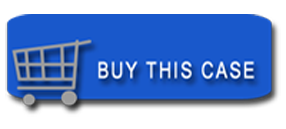
Price: For delivery in electronic format: Rs. 300;
For delivery through courier (within India): Rs. 300 + Shipping & Handling Charges extra
» Enterprise Risk Management Case Studies
» Short Case Studies
» View Detailed Pricing Info
» How To Order This Case » Business Case Studies » Case Studies by Area
» Case Studies by Industry
» Case Studies by Company
Please note:
This case study was compiled from published sources, and is intended to be used as a basis for class discussion. It is not intended to illustrate either effective or ineffective handling of a management situation. Nor is it a primary information source.
Chat with us

Please leave your feedback
|

<< Previous
Introduction
Toyota, the world's third largest car manufacturer after General Motors and
Ford, was rated as the most efficient car maker in the world. Toyota's major
business segments were automotive and financial services.
In 2002, the automotive segment accounted for approximately 90% of Toyota's
total revenues and 96% of Toyota's operating income. The company's
manufacturing, vendor management and product development practices were
considered best in class. Toyota's primary markets (based on vehicle unit sales)
for the year ended March 31, 2002 were: Japan (40%), North America (32%) and
Europe (13%).
|
|
Overview of Major Risks
Toyota believed the profitability of its automotive operations was affected by
factors like
• Vehicle unit sales volumes,
• The mix of vehicle models and options sold,
• The levels of price discounts and other sales incentives and marketing costs,
• The cost of customer warranty claims and other customer satisfaction actions,
• The cost of research and development and other fixed costs,
• The efficient use of production capacity,
• Changes in the value of the Japanese yen and other currencies in which Toyota
did business,
• Intensifying competition,
• Regulatory issues.
|
Risks in Product Development
Product development in the automobile industry was highly capital
intensive and time consuming. Yet, automakers had to keep coming up
with new models from time to time. They had to standardize the core
product, the platform and build features around a small number of
platforms. Toyota was a pioneer in lean product development, a
philosophy which believed in coming up with new products, using
minimum resources. In 1955, when the product development process for
Toyota's model 'Crown'started, the practice of appointing 'susha'(an empowered project manager) to head a project from its inception
was initiated. |
In 1965, Toyota formally established a product planning
division to organize and support sushas. The structure used by Toyota was
essentially a matrix, with functional specialists reporting both to a functional
manager and the susha. The matrix structure helped Toyota to combine the best
features of both functional and divisional organizations. At that time, there
were 10 sushas and 5 to 6 staff members under each susha. Except for replacing
the name susha by 'chief engineer' in 1989, the company did not change the
structure of its product planning division till the early 1990s.
Excerpts >>
|
|